Listen to this article
|
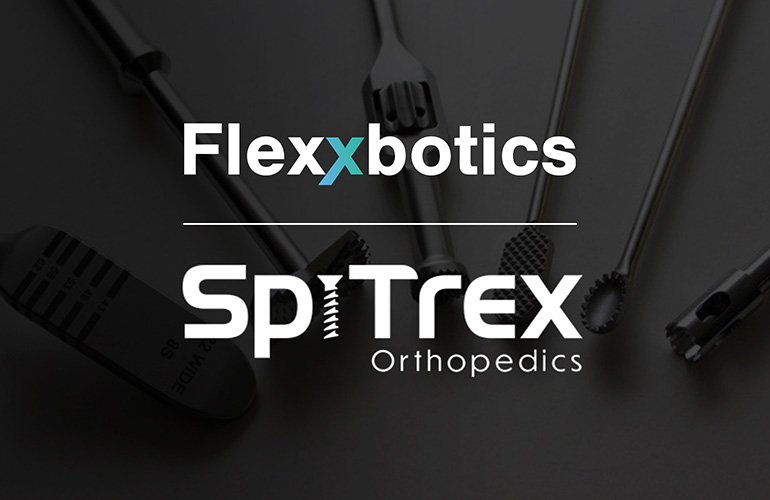
SpiTrex Orthopedics selected Flexxbotics systems to work in its FOBA laser marking work cells. | Source: Flexxbotics
Flexxbotics announced today that SpiTrex Orthopedics, a global medical device contract manufacturer, has chosen its systems for robot-driven manufacturing with autonomous process control. The company’s systems will work in SpiTrex’s FOBA laser marking work cells.
Flexxbotics said its systems enable robots to communicate directly with the FOBA laser marking machines and change jobs in real time within sequence. This direct communication can reduce changeover time at SpiTrex to just 10 minutes, the company claimed.
Before they started using Flexxbotics’ technology, SpiTrex engineers could spend an hour or more setting up a workcell, twice a week, when they need to run a new job.
“The autonomous changeover process, coupled with the closed feedback loop functionality, enables us to produce extremely high-tolerance parts through continuous flow which reduces the overall lead time by 20+%,” said Brett Gopal, SpiTrex Orthopedics senior vice president of operations, in a release. “Flexxbotics directly improves our throughput and ROC [receiver operating characteristic], which in turn increases profitability.”
With the new technology, SpiTrex’s robots can also directly connect with the vision system verifying the laser marking on each part. The robots need to autonomously sort each part based on the results of the vision verification.
Flexxbotics said that by directly connecting robots to vision systems, the company can ensure closed-loop quality for higher yields.
“We are proud to work with SpiTrex as they robot-enable manufacturing operations in their smart factories,” stated Tyler Bouchard, co-founder and CEO of Flexxbotics.
“We understand the necessity for the highest levels of precision while increasing output in advanced machining operations using robotics, particularly in sectors like medical, defense, aerospace and automotive,” he added. “We believe that autonomous manufacturing cannot be achieved without autonomous process control which is why we are focused on robot-machine orchestration.”
Why SpiTrex chose Flexxbotics
There were a number of factors that SpiTrex considered when it chose Flexxbotics. First, the company said it was attracted to Flexxbotics’ ability to autonomously configure a robot and the FOBA laser marker for each job that will run.
SpiTrex also liked its ability to perform closed-loop, in-line inspection with COGNEX’s vision system, which directs the robot to sort parts based on the FOBA marking results and conformance to critical characteristics.
In addition, Flexxbotics offers open connectivity and interoperability between robots. It also supplies FOBA laser markers, and COGNEX vision sensors, along with existing IT business systems.
SpiTrex was interested in the company‘s interchangeable carousels with universal switching processes, which enable quick changeover for faster set-up times. The manufacturer also landed on Flexxbotics because it provides a direct feed of work cell operations and inspection data into quality repository.
Altogether, SpiTrex said that Flexxbotics’ system provided enough flexibility to start with initial work cells, quickly get success, and then scale to additional FOBA laser marking work cells factory-wide.
“Flexxbotics is the only robot machine tending software solution we found capable of delivering the precision, cycle-time and closed-loop compliance required,” Gopal said. “We are impressed with Flexxbotics’ autonomous process control using robots, and the ability to close-the-loop by alerting upstream and downstream workcells of quality problems based on automated inspection results, which is quite unique.”
Inside the implementaton
Bouchard told The Robot Report that SpiTrex didn’t need to make any alterations to its process to implement Flexxbotics’ systems. The company simply needed to add a new in-feed fixture for part presentation to the robots, he explained.
“The project is ongoing with an incremental work cell-by-work cell rollout to all 10 FOBA work cells to reduce disruption,” Bouchard said. “Each work cell takes a business week for initial installation, followed by a production ramp-up optimization period that can range between two to four weeks, depending on the variety and complexity of the parts being processed.”
At SpiTrex’s facility, Flexxbotics’ system directs robots to use COGNEX camera images to determine the pass/fail status of each part. If it detects non-conformance issues that the system needs to correct, It sends alerts with the images to pre- and post-process work cells.
“Human supervision is minimal, with a 10:1 machine-to-operator ratio, where personnel simply stage part lots and then input key variables such as radius, length, and diameter of the parts,” Bouchard said.
Tell Us What You Think!