Listen to this article
|
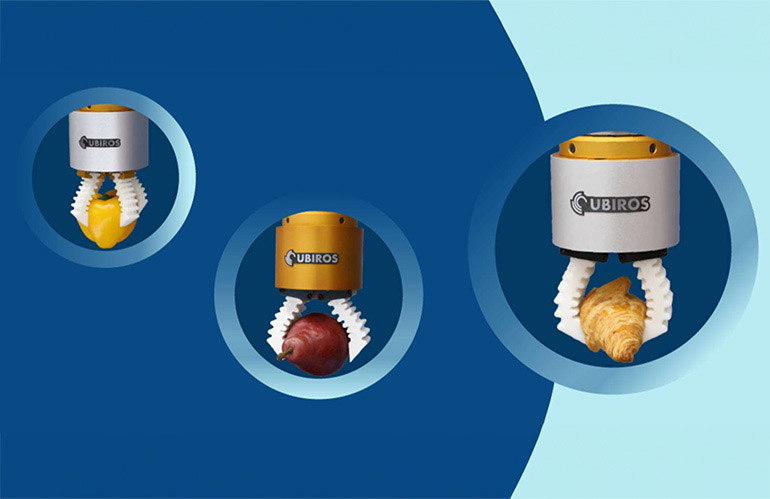
The Gentle Duo Mini soft grippers are suitable for food handling. Source: Ubiros
Reliable and delicate robotic grasping has long been a challenge, but Ubiros Inc. said it can solve the problem without the bulky pneumatics or complex coding of previous approaches.
The company’s electrically driven and modular grippers are easier to deploy and use than other soft grippers, according to Onder Ondemir, president of Ubiros. He is also a professor in the engineering department at Northeastern University.
Ubiros offers the Gentle Flex Module and Gentle Flex CC for users that want to build their own grippers. The spinout of Worcester Polytechnic Institute (WPI) also offers Gentle Duo with two soft fingers and Gentle Pro with four fingers, as well as Touch models for both that include force control, part sensing/confirmation, and a low-power mode.
The Natick, Mass.-based company said its compliant grippers are suitable for food handling and packaging, textiles, and some warehouse applications. Ubiros, which is a resident startup at MassRobotics, already has distributor agreements in China, South Korea, Turkey, the U.K., and the U.S.
Founder fascinated by technology
“I loved Knight Rider as a kid and asked my mom, ‘Who makes [smart car] KITT? What do I need to become to make something like that?’” recalled Ondemir. “She said ‘mechanical engineer.’”
“I grew up and became an industrial engineer, but I’ve always been fascinated with mechanical systems,” he told The Robot Report. “I worked at an insurance company modeling the capacity of systems and demand forecasts, and I became a vice president.”
Ondemir later ran into a friend [Cagdas Onal] who was doing post-doctoral associate work at MIT and collaborating with Harvard University researchers working on soft robotics.
“We knew the limitations of pneumatics – precision is low, control is hard, and the equipment needed to generate compressed air uses a lot of electricity,” he said. “After spending years in the lab, one day, he came to me and said, ‘Onder, I think I have groundbreaking technology for packaging and gripping in general, but I don’t want to run the company.’ Becoming the CEO was a no-brainer to fulfill my desire to build machines and work with my friend.”
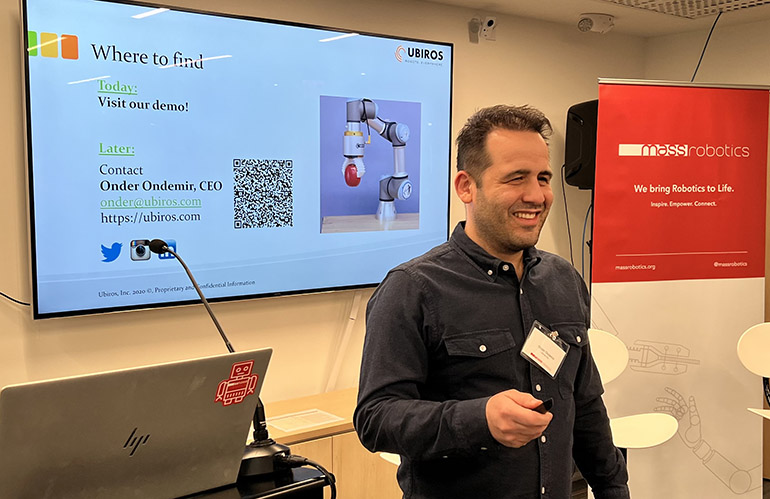
Ubiros President Onder Ondemir at MassRobotics. Source: Ubiros
The genesis of Ubiros
Ubiros has largely focused on food handling.
Automating the handling of fruit and baked goods is not easy, because such delicate food items are easily damaged, Ondemir noted. Rigid grippers typically don’t have sufficient sensitivity, and many other companies are trying to solve problems such as object detection and singulation, he said.
“In farming, crops are being left to rot in the field, which is a huge waste,” added Ondemir. “A key barrier to getting automation is handling food with a soft touch.”
“But the real problem we’re solving is the worker shortage,” he said. “Harvesting and packing jobs aren’t interesting to people, and there are the issues of efficiency for the employer – most people work one shift – and also injuries and finally the cost of food.”
Fingers versus suction cups
For most applications where similar items are picked, suction cups are sufficient, said Ondemir. However, when there’s clutter, such as in e-commerce bins, or tight spaces like bookshelves, picking then requires a combination of sensing to identify each object and the ability to singulate that object.
Suction cups are versatile, but porous, dusty, fragile, or oddly weighted items are not always suitable for suction cups, Ondemir observed.
“We’re proud to be one of the few companies developing individual finger actuation rather than the whole hand,” he said. “For singulation, it can provide alternatives in complex picking situations.”
Ubiros Gentle grippers promise benefits
Ubiros’ Gentle grippers use electric servo motors and a cable-driven system similar to the tendons of the human hand.
“The difficulty in designing the system was maintaining softness while mechanically operating the finger – that’s where our patent is,” Ondemir said. “Our technology allows the finger unit to be flexible in the grasping direction but very rigid in twisting or bending sideways.”
Electric end-of-arm tooling (EOAT) removes the need for tubes, valves, and compressors, he said. Also, while pneumatic systems need to cycle to attempt another grasp, an electric one can reposition more quickly.
In addition, electric grippers have instant torque rather than needing to build up pressure for heavy payloads as hydraulic or pneumatic systems do, said Ondemir.
Up to 35% of the electricity bill in factories is spent on pressurized air, and 40% of the battery life of a mobile manipulator is consumed by a suction cup, he asserted. Thus, Ubiros’ grippers could save a lot of battery power for autonomous mobile robots (AMRs) or drones, Ondemir said.
Is Ubiros looking at mobile manipulation?
“We’ve had serious conversations with Staubli,” Ondemir replied. “Our gripper would be in addition to its existing arm and base, unlike others.”
In addition, United Robotics Group has integrated Ubiros’ gripper with a mobile manipulator that will be demonstrated at Automate.
Ondemir surveys tech trends
Beyond mobile manipulation, Ondemir relied on his experience in robotics development to comment on current tech trends.
“Artificial intelligence and machine learning allow us to implement predictive maintenance,” he said. “Our electrical micro-controller is partly a system for force control and partly sensing. It’s able to collect temperature data from inside the gripper, plus cycle counts and electric current to build models to predict failures. That’s in our roadmap.”
Ubiros is not currently working with digital twins because it’s difficult to know the actual deflection of soft objects and where something is in space, acknowledged Ondemir. A lot of research is being devoted to this topic, he said.
What about humanoids? “They’ll have to have soft components for safety and to guard against falling,” Ondemir said. “This will be a key use for soft robotics in general, not just soft grippers. Because we’re a spinoff of WPI, we already have soft 3D sensors and a patented design of a soft arm, but there’s a lot still to do.”
Mechanical intelligence for manipulation
“The idea behind what we call ‘mechanical intelligence’ is that if you can mechanically achieve something, you need expensive programming, motion control, and vision less,” said Ondemir. “We built something that is under-actuated, with fewer motors to move the joints. Electric actuation allows us to have full-bodied fingers rather than hollow ones that can be punctured or leak in otherwise sanitary environments.”
“Depending on the shape of the object, the gripper can automatically conform to it. It’s more forgiving of inaccuracies, and you don’t need extreme precision,” he continued. “Because the grippers bend themselves over an object like an egg or an apple, the force is distributed over a larger area.”
Ubiros did build some force control into its Gentle grippers, allowing users to increase or decrease pressure, but it’s not necessary in most cases, Ondemir said.
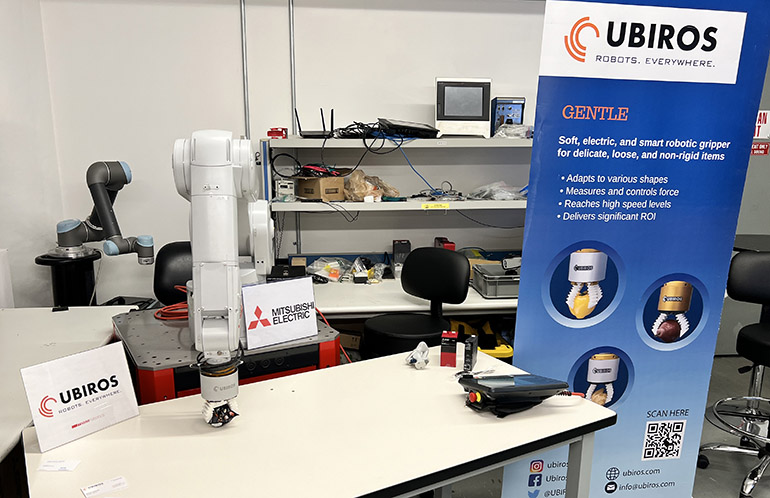
Ubiros and its partners recently participated in a MassRobotics Demo Day. Source: Ubiros
Ubiros looks ahead
The Gentle gripper is initially tackling labeling and grading of tomatoes and cucumbers, and Ubiros has received a lot of interest recently from bakeries, said Ondemir. A hygienic gripper could then address handling of raw beef, poultry, and fish.
To that end, Ubiros is looking for funding to make its grippers more hygienic and robust against cleaning agents. It is working on safe-food handling certifications.
On the industrial side, Ubiros is conducting a pilot with Mitsubishi to handle a variety of objects and manage robot grasping through Mitsubishi’s teach pendant.
“Down the road a few years, we want to focus more on the data side, allowing customers to access data through the end effectors,” Ondemir said. “We plan to eventually bring other patented technologies into the workplace – 3D sensors, haptic gloves, human-in-the-loop systems, remote manipulation, and soft arms.”
Ubiros will be at the Robotics Summit & Expo next week and Automate the week after that.
Tell Us What You Think!