Listen to this article
|
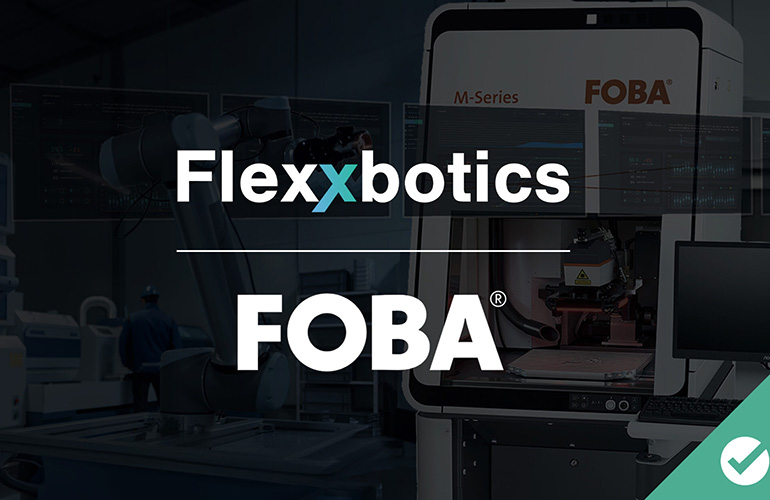
Flexxbotics’ system is now compatible with FOBA Laser Marking + Engraving equipment. | Source: Flexxbotics
Flexxbotics has announced that its robotic technology is now compatible with FOBA Laser Marking + Engraving products for machine tending. This includes communication with FOBA’s integrated camera system for vision-based inspections.
With Flexxbotics’ robot-driven operation of FOBA equipment, customers can achieve continuous operation, greater throughput, and higher yields, asserted the company. In addition, the integration offers closed-loop feedback to the robot for autonomous process control, it said.
“Combining FOBA with Flexxbotics is particularly valuable in industries with strict regulatory compliance requirements that dictate the highest levels of repeatable precision, such as medical devices and surgical products, along with aerospace, defense, and space,” said Tyler Bouchard, co-founder and CEO of Flexxbotics, in a release.
“Environments that require rapid and accurate processing like semiconductor and electronics operations also benefit substantially,” he said. “With Flexxbotics and FOBA together, customers can optimize cycle time, expand capacity, and increase profit per part.”
Compatibility promises more flexibility, faster deployments
FOBA Laser Marking + Engraving, a brand of ALLTEC Angewandte Laserlicht Technologie GmbH, provides laser marking systems and laser engraving machines. Its offerings include fiber laser markers and UV laser markers, ultrashort pulse laser markers, CO2 laser markers, and green laser markers for a range of applications and industries.
Flexxbotics said its patent-pending FlexxCORE technology enables robots to securely connect and communicate with FOBA laser marking and engraving equipment. This compatibility includes the FOBA MarkUS control, its digital I/Os, PROFINET, Profibus/TCP/IP, and EtherCAT.
FlexxCORE can coordinate robot actions with FOBA’s three-stage marking process. This includes part inspection before marking, automatic mark alignment, and subsequent validation of the marking, noted the Boston-based company.
The system uses either the Intelligent Mark Positioning (IMP) or Point & Shoot (P&S) capabilities in the FOBA equipment for precise alignment of the laser marker on the customer’s product. It also allows for vision-assisted workflows if needed for accuracy, said Flexxbotics.
“Connecting robotic machine tending with our FOBA laser-marking solution using Flexxbotics provides an even greater return on investment,” stated Jeffrey A. Kniptash, FOBA’s sales manager for Americas. “Enabling Flexxbotics robot-driven manufacturing with our FOBA laser marking and engraving equipment to enable autonomous process control can remove bottlenecks and deliver continuous operation.”
Flexxbotics aims for robot-driven manufacturing at scale
Flexxbotics claimed that its “workcell digitization technology is the backbone of the smart factory,” and key to achieving robot-driven manufacturing at scale. It said its software-as-a-service (SaaS)/hybrid architecture runs both online and offline, so production can continue with or without Internet access.
FlexxCORE also works with existing automation equipment, IT systems, and people, said the company. Last week, Flexxbotics announced compatibility with Makino machine tools. It previously noted that FlexxCORE works with HURCO CNC machines and automation, as well as with Nakamura-Tome machine tools.
A full set of bidirectional communication, transform, and routing capabilities are available in FlexxCORE for connected robots and FOBA equipment. This includes loading programs, sending instructions, updating parameters, and status awareness depending on the equipment’s capabilities, said Flexxbotics. It said this allows the robots to command the smart factory machinery.
The company plans to demonstrate its technologies at ATX West from Feb. 6 to 8 in Anaheim, Calif.
Tell Us What You Think!