For today’s heavy manufacturers, conveyance automation systems must be extremely robust and capable of transporting high-capacity payloads, yet also deliver the high levels of flexibility, safety and scalability expected from today’s mobile robotic systems. Modern automated guided vehicles can do just that.
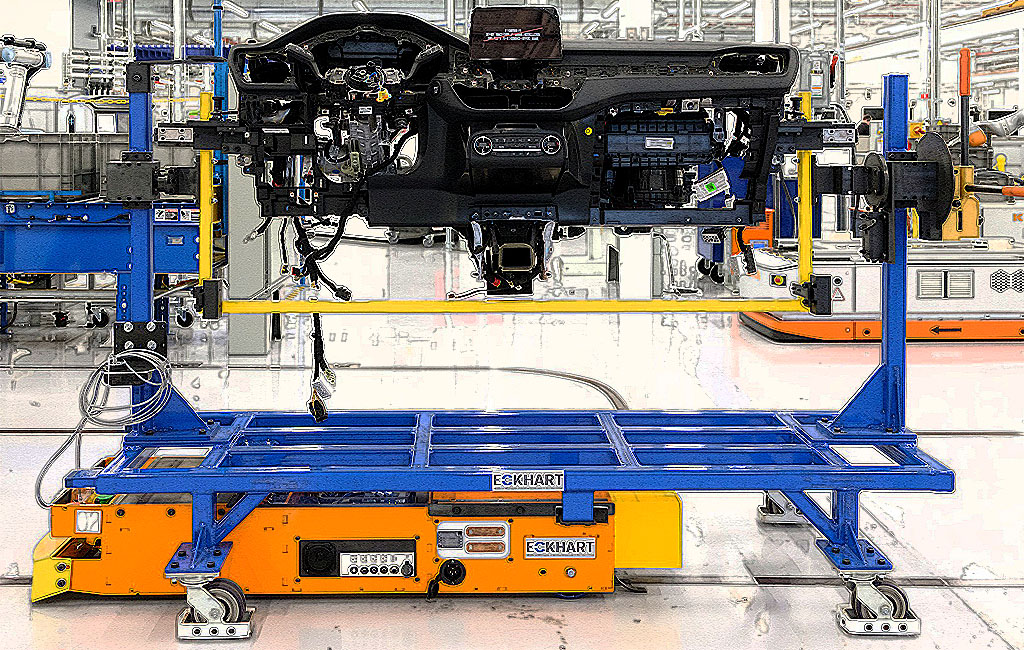
Listen to this article
|
Manufacturing facilities continue to increase their levels of automation to reduce costs, improve productivity, and increase operational efficiency. Newer forms of automation technology also provide manufacturers with a high degree of flexibility, a capability lacking in many earlier forms of fixed, or ‘hard’, automation.
These flexible automation solutions are being embraced by manufacturers as a key strategic differentiator and business facilitator. For today’s manufacturers, “flexibility is the new productivity”.
Manufacturing Automation
Manufacturing automation can take many forms. The use of reprogrammable, articulated robots, and now including collaborative robots, for applications such as welding, painting, and palletizing is common among manufacturers of all types and sizes, and other use cases like conducting quality checks using robotic vision inspection systems continue to expand. Another manufacturing automation mainstay involves the use of technologies for conveyance, the act of transporting materials, parts and other objects, as well as moving items under construction in assembly lines for sequential manufacturing processes.
Conveyance Automation Types
In broad terms, automation solutions for manufacturing conveyance are of two types – Fixed Conveyance Systems and Flexible Conveyance Systems.
- Fixed Conveyance Systems – As their names imply, fixed conveyance systems are automation technologies that are immovable once in place, or can only be redeployed at the expense of disruption and great cost. Fixed conveyance systems such as belts, rollers, and overhead conveyors, provide manufacturers with productivity benefits, but at the expense of flexibility. Towline conveyors (see below), commonly used for moving heavy loads in manufacturing facilities, are another form of fixed conveyance solution.
- Flexible Conveyance Systems – Automation technologies that can be flexibly redeployed once installed, such as Automated Guided Vehicles and Autonomous Mobile Robotics (see below), have found wide use in applications like delivering kitted materials to point-of-use on an assembly line, as well as transporting product like cars, trucks, and tractors through their assembly processes. Autonomous mobile robots are commonly used as an alternative to fork trucks and are typically tasked with transporting components as part of lineside replenishment operations for electric vehicles, agricultural equipment, and medical device manufacturers. Automated guided vehicles have seen wide adoption among manufacturers of heavyweight products because of the safety advantages that come with automation technologies over manual options.
Conveyance Automation
Prior to the development of automated conveyance solutions, items under manufacture were typically transported manually using carts, trolleys or forklifts, both powered and unpowered. Over time, many of these manual conveyance platforms – inefficient and often dangerous – were automated using a variety of system types including:
- Towline Conveyors – Conveyors have been employed in manufacturing plants for over 100 years. One form of these systems, towline conveyors (tow conveyors, towveyors, build line conveyors, trac-veyors), have found wide use for manufacturing processes that require constant forward motion for progressive operations. The majority of towline conveyor systems in manufacturing environments use a recessed towline (usually a chain) to pull wheeled carts along a fixed path through sequential workstations.
The development of towline systems requires substantial construction and engineering of their operational environment. Deep trenching in the floor and extensive concrete / civil work is often required. Reconfiguring traditional chain-based towlines in response to changing business requirements is a very labor-intensive, costly and lengthy undertaking.
AGVs move with precisely calibrated acceleration and deceleration, and employ different sensing technologies to detect people and obstacles, slowing down or stopping depending on how near the object is, and resuming again when the path is clear.
- Automated Guided Vehicles (AGVs) – Automated guided vehicles (AGVs), are mobile robots that use magnetic tape, RFID tags, optical strips, lasers, or other modalities to guide them through facilities along pre-determined pathways. AGV navigation paths can be altered with relative ease by relocating the guides that control the systems. Modalities like magnetic tape represent the lowest cost, but highest maintenance approach to navigation.
AGVs are a common (and proven) form of robotic conveyance in manufacturing environments for applications such as parts and components delivery. Since AGVs are designed to move continuously along a fixed path, it also makes them extremely well suited as a replacement for traditional conveyor systems for work-in-process movement during manufacturing operations. Further, since each AGV unit can be individually controlled, it is possible to de-couple the assembly line. For example, some manufacturers strategically plan for buffers, queue positions, or in-process kanbans (IPKs), to help smooth station-to-station timing imbalances. AGVs, being de-coupled from the unit ahead of it, are able to progress out of a completed work station to the buffer to keep the line moving if the next station may be temporarily blocked.
Autonomous guided vehicles range in type from lightweight ‘tugger’ AGVs that pull unpowered carts for transporting loads, to heavy-duty, high payload systems (‘unit load’ AGVs) that can transport discrete, multi-ton objects. Unit load AGVs are also increasingly being utilized to move heavy products under manufacture from one fabrication stage to another.
AGVs move with precisely calibrated acceleration and deceleration, and employ different sensing technologies to detect people and obstacles, slowing down or stopping depending on how near the object is, and resuming again when the path is clear. Recently, some AGVs have incorporated technologies such as vison systems and LiDAR allowing them to navigate autonomously in a manner similar to autonomous mobile robots (see below).
- Autonomous Mobile Robots (AMRs) – A relatively new form of conveyance automation – autonomous mobile robots – have been widely embraced in warehouses and distribution centers (DCs) to improve the efficiency of e-commerce inbound (‘putaway’) and outbound (‘picking’) fulfillment operations. While there has been much discussion concerning the use of autonomous mobile robots for industrial work, the technology is still in the relatively early stages of adoption. In manufacturing settings, common AMR applications include the use of deck-load mobile robots to deliver components and subassemblies to workstations, or as tuggers for lightweight carts.
AMRs navigate autonomously using a variety of sensors and sensing technologies including LiDAR (2D or 3D) and camera systems (again, 2D or 3D), with many utilizing both, plus some other types of proximity sensors. AMRs utilize their sensors to detect its surroundings and choose the most efficient route to the target. It works completely autonomously, and if forklifts, pallets, people, or other obstacles occur in front of it, the AMR will safely maneuver around them, using the best alternative route.
For manufacturers, increasing ‘safety’ is positively linked to various business value drivers. Examples include improved worker retention, lower operational costs, and increased production efficiency.
Selection Criteria
Many factors must be considered when selecting manufacturing conveyance automation solutions, including the following critical elements:
- Capacity – In the context of manufacturing conveyance automation, capacity refers to two distinct properties:
- Payload Capacity – Payload capacity refers to the total amount of weight that towline carts, AGVs an AMRs can carry. Currently, the payload capacity of towline and AGV conveyance platforms exceed that of autonomous mobile robots. For heavy load manufacturing operations, where the parts and objects under assembly often exceed 10,000 lbs., high-capacity towline solutions and AGVs are the only choice.
- Towing Capacity – Towing capacity denotes to the amount of load weight towline conveyors, AGVs and AMRs can pull.
- Flexibility – In order to respond to changing business requirements and fluctuations in demand, manufacturers are placing greater emphasis on flexible conveyance systems, and eschewing solutions that rely on ‘hard’ automation and expensive, fixed infrastructure. Manufacturers are increasingly looking to avoid new projects with extensive civil work that will “lock in” their facility layout for years to come. Conveyance systems differ on their level of support for flexibility which can take many forms including:
-
- Deployment Flexibility – The ability to deploy manufacturing conveyance systems rapidly and at low cost, is a key requirement for today’s agile manufacturers. Manufacturers should also be able to redeploy or relocate conveyance automation solutions within manufacturing sites with minimal operational disruption and cost.
- Application Flexibility – Application flexibility refers to the ability to repurpose conveyance platforms for different applications, processes, or operations. For example, most AGVs are customizable so that they can be modified to meet specific application needs or ergonomic requirements. Common customizations include the addition of load-handling carrier frames, lift decks, scissor lifts, powered trunnions, and turntables.
- Scaling Flexibility – Scaling flexibility refers to the capacity to increase or decrease the number of operational conveyance systems depending on need. For example, when using automated guided vehicles for sequential manufacturing operations, the workflow can be increased or decreased easily by adding or removing AGVS from the line. For manufacturers that have demand that is seasonal or difficult to predict, addition or subtraction of workstations.
-
- Safety – Safety is a key driver for increasing levels of conveyance automation in manufacturing sites and elsewhere. Compared to manual systems, for example, AGVs have proven to reduce worker injury, and decrease damage to parts, products, and infrastructure. They can detect objects in operational range and slow to stop or avoid them. Systems are also equipped with safety edges and bumpers, along with anticipatory warning systems using lights and sounds to let workers know of their approach.
For manufacturers, increasing ‘safety’ is positively linked to various business value drivers. Examples include improved worker retention, lower operational costs, and increased production efficiency.
- Efficiency and Quality – For manufacturers, improved productivity – increasing the quantity of the products they deliver – is often given as the primary benefit for automating their production processes. While true, is not the whole story. Increasing efficiency, that is, increasing the effectiveness of manufacturing operations, as well as improving and the quality of the items produced (while minimizing costs), is equally important.
Conveyance solutions such as automated guided vehicles are not automation islands. In manufacturing sites, fleets of AGVs are monitored and controlled by sophisticated software, and often linked to warehouse management systems (WMS) and Manufacturing Execution Systems (MES). AGV management software can dynamically respond to feedback from production lines to improve operational efficiency by optimizing performance, streamlining workflows, and eliminating chokepoints. Software such as Ignition, Wonderware, Aveva, and PLEX provide directives to an AGV fleet both wirelessly and through commonplace Allen-Bradley or Siemens PLCs.
The use of autonomous guided vehicles in manufacturing environments has been proven to increase the consistency and reliability of operations, which has a positive impact on quality of produced goods. AGVs provide autonomous and dependable point-to-point transportation of goods and material, and by doing so, it dramatically reduces the potential for human error, the primary source of industrial accidents and damage to products, facilities and more. Furthermore, since AGVs are programmatically controlled, and highly integrated with governing software systems, the AGV units can be programmed to only move if specific quality criteria are met, effectively serving as an in-station poka-yoke.
Many manufacturers need to convey and assemble products that weigh 20,000 lbs, 30,000 lbs, and up to 50,000 lbs, but AGVs with capacity in this range are rare.
Automating Heavy Load Conveyance
For industries, such as the electric vehicle, aerospace, alternative energy, and defense sectors, manufacturing processes often involve the movement of heavy parts, objects in work, and eventually, finished products. As such, the capacity of conveyance automation systems for these manufacturers must often exceed 10,000 lbs. Many manufacturers need to convey and assemble products that weigh 20,000 lbs, 30,000 lbs, and up to 50,000 lbs, but AGVs with capacity in this range are rare. The unique load requirements for these ‘heavy’ manufacturers, is very different for other classes of manufacturers, and is a key differentiator when evaluating conveyance automation solutions.
AGVs vs Towlines
High-payload AGVs and towlines both share the ability to move heavy items sequentially along manufacturing work lines. Automated guide vehicles, however, have distinct advantages over older towline approaches. AGVs, for example, can be deployed without the high cost of building the fixed towline infrastructure, including the entrenching required for embedding the towline itself.
Automated guided vehicles also provide much greater levels of flexibility compared to towline conveyors. Production lines can be installed rapidly and modified easily to meet the demands of periodically changing assembly lines in accordance with agile methods.
AGVs vs AMRS
Automated guided vehicles and autonomous mobile robots provide manufacturers with many advantages over towline conveyance solutions. Each delivers high levels of flexibility and safety. AGVs and AMRs deployments can also scale as need dictates. However, the distinctive capacity requirements for heavy load manufacturing – 10,000 lbs. and greater – places AMRs at a distinct disadvantage as an automated transportation option for this class of production. For safety, an ultra-heavy product should typically be assigned to a predefined and fixed travel path without latitude given to a navigation technology to identify and pick alternative routes.
Best of Both Worlds
Manufacturers are increasingly turning to automation and robotics technologies to address the many new challenges brought on by rapid business change, sector growth and increased competition. This includes manufacturers in the medical device (think MRIs), commercial trucks, spaceflight, recreational vehicles, and other heavy industries.
In the past, these manufacturers turned to towline systems to automate their production lines. Towline systems, robust and capable for moving heavy loads, lack the flexibility inherent in more modern automated conveyance solutions such as AGVs and AMRs.
Autonomous mobile robots, a relatively recent addition to the manufacturer’s solution set, are noted for providing high levels of deployment flexibility, application flexibility, and scaling flexibility. While these systems deliver value as transportation platforms in manufacturing facilities and warehouses, their payload and towing capacities fall short for production workflows that demand the movement of heavy loads.
Modern automated guided vehicles combine the capabilities set of autonomous mobile robots – flexibility, safety and scalability – with the load capacity of towline conveyors. As such, they provide manufacturers with the best of both worlds, a cost-effective, flexible, heavy-load conveyance solution for production build lines designed for manufacturing as it is done today, and that can meet the manufacturing demands of tomorrow.
Sponsored content by Invio Automation
About the Author
Dan Kara is the former Vice President of Robotics at WTWH Media where he chartered with driving the company’s robotics initiatives including the Robot Report and Robotics Business Review online portals and the Robotics Summit Conference and Exposition, Healthcare Robotics Engineering Forum, RoboBusiness Conference & Expo and the International Field Robotics Engineering Forum. Prior to joining WTWH, he was Practice Director, Robotics and Intelligent Systems at ABI Research. Dan was also President of Robotics Trends, an integrated media and research firm serving the personal, service and industrial robotics markets. Dan has also worked as Executive Vice President of Intermedia Group, and Director of Research at Ullo International.